Во областа на обезбедувањето и контролата на квалитетот, особено во индустриите како што се производството, воздушната и здравствената заштита, термините „инспекција“ и „тестирање“ често се користат наизменично. Сепак, тие претставуваат различни процеси, особено кога станува збор за напредни технологии како што сеРендгенски системи за инспекција. Целта на овој напис е да ги разјасни разликите помеѓу инспекцијата и тестирањето, особено во контекст на системите за инспекција со рендген, и да ги нагласи нивните соодветни улоги во обезбедувањето квалитет и безбедност на производот.
Системите за инспекција со рендген се метод на недеструктивно тестирање (NDT) кој користи технологија на рендген за да ја испита внатрешната структура на објектот без да предизвика никаква штета. Овие системи се широко користени во различни индустрии како електроника, автомобилска и видео амбалажа за откривање на дефекти како пукнатини, празнини и туѓи предмети.Главната предност на инспекцијата со рендген е неговата способност да обезбеди детална слика за внатрешните карактеристики на производот, што може темелно да се анализира за неговиот интегритет.
Процес со кој производ или систем се проверува во комората за инспекција за да се осигура дека ги исполнува бараните стандарди или спецификации. Во еденСистем за инспекција на рендген, инспекцијата вклучува визуелна или автоматска анализа на генерираните рендгенски слики. Целта е да се идентификуваат какви било аномалии или дефекти кои можат да влијаат на квалитетот или безбедноста на производот.
1. Цел: Примарната цел на инспекцијата е да се потврди усогласеноста со однапред одредени спецификации. Ова може да вклучува проверка на физичките димензии, завршетокот на површината и присуството на дефекти. 2.
2. Процес: Инспекцијата може да се направи визуелно или со автоматизирани системи. Во инспекцијата со рендген, сликите се анализираат од обучени оператори или напреден софтвер за да се идентификуваат какви било аномалии. 3.
3. Резултат: Резултатот од инспекцијата обично е одлука за полагање/неуспех врз основа на тоа дали производот ги исполнува или не воспоставените стандарди. Доколку се најдат дефекти, производот може да се одбие или да се испрати на понатамошна евалуација.
4. Фреквенција: Инспекцијата обично се врши во различни фази од производствениот процес, вклучувајќи инспекција на дојдовен материјал, инспекција во процесот и инспекција на финалниот производ.
Тестирањето, од друга страна, ги оценува перформансите на производот или системот под специфични услови за да се утврди неговата функционалност, доверливост и безбедност. Во случај на системи за инспекција со рендген, тестирањето може да вклучи проценка на перформансите на системот, неговата калибрација и точноста на резултатите што ги произведува.
1. Цел: Примарната цел на тестирањето е да се процени оперативната способност на системот или производот. Ова вклучува проценка на способноста на системот за инспекција на Х-зраци да открие дефекти или точноста на направените слики. 2.
2. Процес: Тестирањето може да се изврши со користење на различни методи, вклучувајќи функционално, стрес и тестирање на перформанси. За системите за инспекција со рендген, ова може да вклучи водење примерок од познати дефекти низ системот за да се процени неговата способност да ги открие.
3. Резултати: Резултатот од тестот е обично детален извештај во кој се наведени показателите за перформансите на системот, вклучувајќи ја чувствителноста, специфичноста и севкупната ефикасност во откривањето на дефектите.
4. Фреквенција: Тестовите обично се изведуваат по првичното поставување, одржување или калибрација на системот за инспекција на Х-зраци и се изведуваат периодично за да се обезбеди континуирано функционирање на системот.
Дозволете ни да воведеме една од нашите компанииСистем за инспекција на рендген
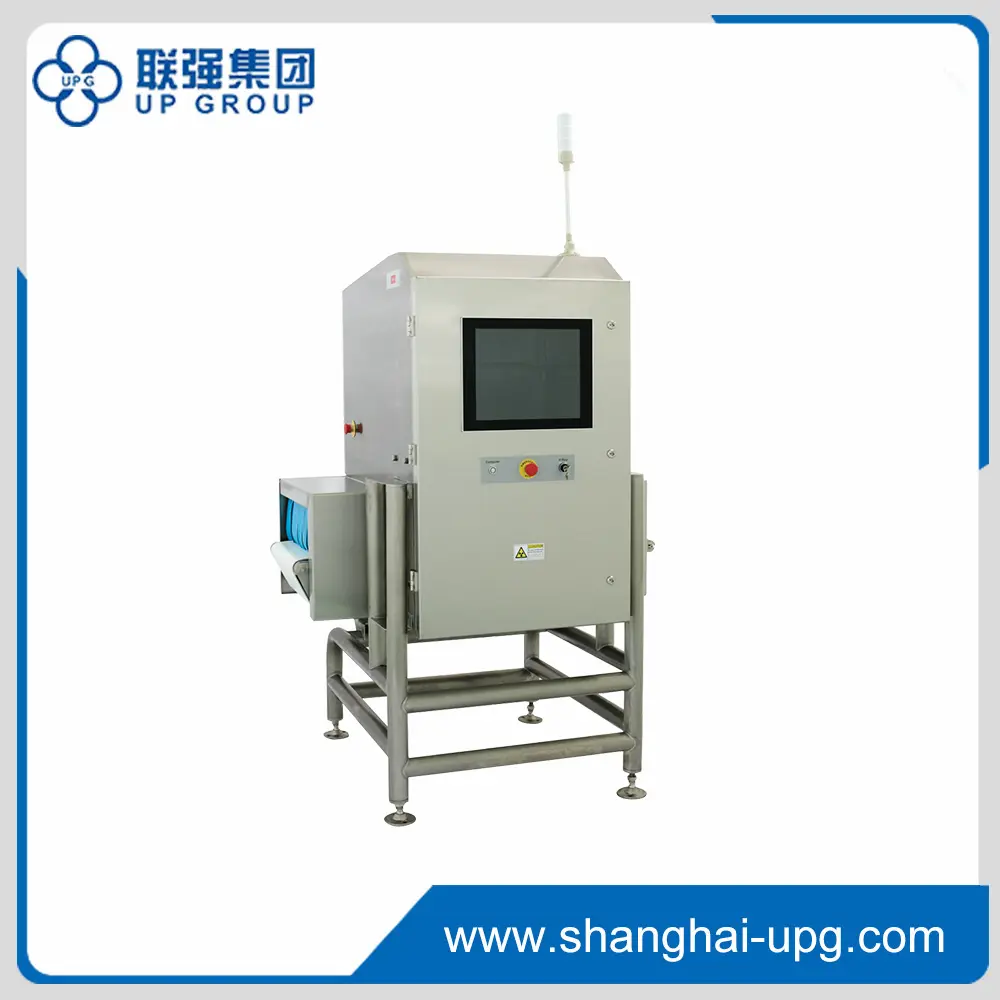
Засновано на интелигентни алгоритми за препознавање странски објекти со одлична софтверска самоучење и точност на откривање.
Откријте туѓи предмети како што се метал, стакло, камена коска, гума со висока густина и пластика.
Стабилен механизам за пренесување за подобрување на точноста на откривање; флексибилен преносен дизајн за лесна интеграција со постоечките производни линии.
Достапен е широк опсег на модели, како што се алгоритми за вештачка интелигенција, алгоритми со повеќе канали, модели со тешки модели со широки модели, итн. за да се подобрат перформансите и да се намалат трошоците за производство на локацијата.
Иако инспекцијата и тестирањето се важни компоненти на обезбедувањето квалитет, тие служат за различни цели и се изведуваат поинаку, а еве некои од клучните разлики:
1. Фокус: Инспекцијата се фокусира на проверка на усогласеноста со спецификациите, додека тестирањето се фокусира на проценка на перформансите и функционалноста.
2. Методологија: Инспекцијата обично вклучува визуелна анализа или автоматска анализа на слики, додека тестирањето може да вклучува различни методи за оценување на перформансите под различни услови.
3. Резултати: Резултатите од инспекцијата обично поминуваат/не успеваат, додека резултатите од тестот обезбедуваат длабинска анализа на функционалноста на системот во форма на извештај за перформансите.
4. Кога: Инспекцијата се врши во различни фази на производство, додека тестирањето обично се врши при поставување, одржување или периодична евалуација.
Како заклучок, и инспекцијата и тестирањето играат витална улога во ефективната употреба наСистем за инспекција на рендген. Разбирањето на разликата помеѓу овие два процеси е од витално значење за професионалците за обезбедување квалитет и контрола. Инспекцијата осигурува дека производите ги исполнуваат специфичните стандарди и упатства, додека тестирањето ги оценува перформансите и доверливоста на самиот систем за инспекција. Со користење на двата процеса, бизнисите можат да го подобрат квалитетот на производот, да обезбедат безбедност и да одржуваат усогласеност со индустриските стандарди. Како што технологијата продолжува да напредува, инкорпорирањето на напредните системи за инспекција на Х-зраци во времето за обезбедување квалитет несомнено ќе игра клучна улога во иднината на производството и другите индустрии.
Време на објавување: 21-11-2024 година